Yes, an interesting read, but a somewhat difficult one at 5 pages; (may say more about my own attention span).
I have to admit that I don't know much about David Heraldson motorcycles, but I have seen fake DH sprockets, too pricey (way).
After reading one time, I am still not sure if the
consensus was that the originally posted Higgins badge was a nice fake; or whether consensus even mattered.
I did not read anyone questioning the false premise of the OP question, of why (besides the obvious profit motive) would a counterfeiter take such painstaking measures to fake a badge that looked fake. I believe that the OP partially answered the question, "make every attempt to make it look as close to the original or what others perceived as original, as possible". So there's two factors, the 'as possible' part (cheapest cost) and the 'what others perceived as original' (faking it part). There may also be an old-Abe cliché about some people, sometimes, which may play into the business model for counterfeiters.
The Higgins badge had the right shape and number of holes, so it meets the "Ritz cracker test". The Higgins badge spelt all of the English words correctly, so a foreign-made fake may be ruled-out. I would suggest that the Higgins badge does not look so fake, and it looks just like what others may perceive as original, (unless they live for the CABE). Perhaps a more difficult to suspect counterfeit, might also be more difficult (costly) to manufacture. A buyer may pay more for better-looking fakes, but I would think that there might be a considerable discount between close fakes and originals, (if known).
Also, I did not read any estimates on the prices of the non-shiny old-looking fakes; the most accurate price estimates are actuals paid, ($20?).
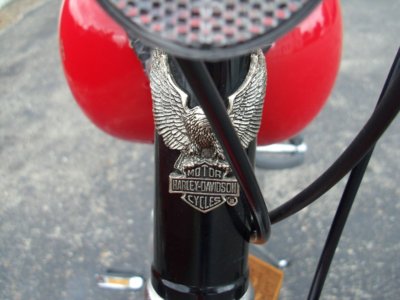
Another interesting part to me was the manufacturing method discussion. One summer, I worked for a tool & die maker in a small machine shop; I operated the two-hand cutting and stamping press (and I still have 10 digits), a bending/shaping hand press, pantograph engraving machine, polishers, and the oxygen-acetylene silver-brazing and glass-enameling (cloisonné) torch. I also had school projects using acid etching methods (thick film technology). Later, I would work for a much larger organization, with too many co-workers missing fingers, toes, or hearing.
Most classic badges that I see are made from stamping brass sheet metal into a die, or more modern by the acid etch method. Casting molten (that means melted into a hot liquid) metal into a mold seems highly-archaic, maybe for ToC bikes; (then there is also a sintering process); I also have a couple thinner badges embossed from a thick metal foil material.
The 1st step in stamping was cutting the pieces from a sheet or strip of brass (please don't get me started on the brasses and bronzes, reds and yellows, leaded and unleaded, or copper alloys). Those 1st pieces would be cut as closely together as possible, in cookie-cutter fashion, to reduce the amount of wasted material.
They would be cut to the outside shape or profile of the finished stamping, and fit into the stamping die of the next step. With the machine reset for the stamping operation (shaping die), the process was repeated, except the output would have the desired shape and contours, but also some excess metal squeezed to the outsides (it had to go someplace under the pressure). [An alternative was to sometimes stack two pieces, resulting in one piece with a concave back (more lightweight) and the other bent piece to be the next one shaped, not wasted]. Sometimes stamping two times was necessary for a thinner output, (or maybe the machine needed adjustment to hit harder). A repeat of the 1st cutting step would trim-away the excess metal, and after polishing, acid-pickling and scrubbing, the pieces would then be ready for enameling. I like the two variations of stippling on the embossed badges.